
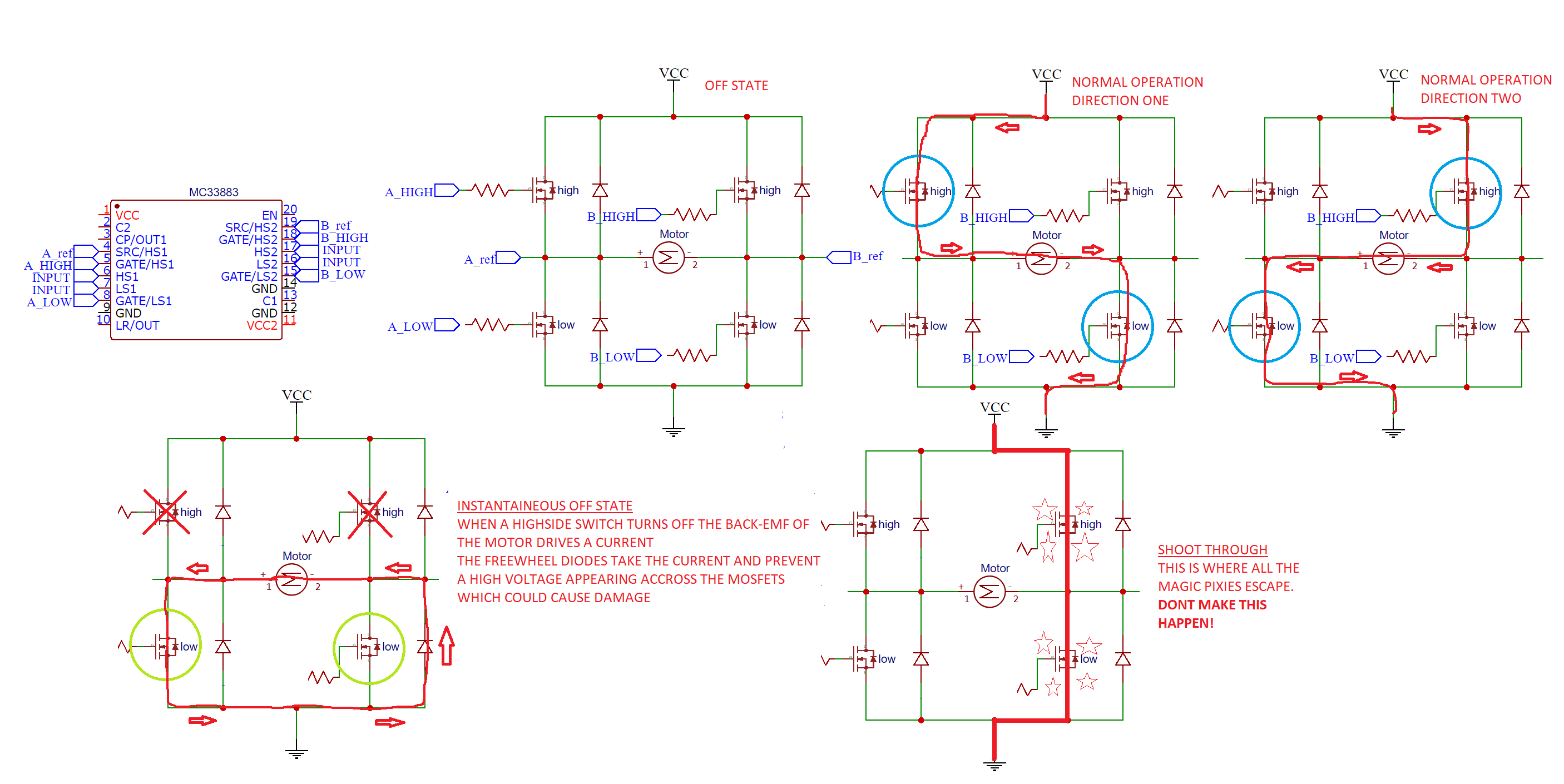
#FULL BRIDGE MOSFET DRIVER 5V FREE#
If you have any doubts, feel free to ask. Of course the capacitor must be large enough that the potential difference across it doesn't drop too low for the MOSFET drive. The capacitor -ve is connected to VS which is the MOSFET source and so, the MOSFET gate is driven with a voltage higher than MOSFET source by as much as (VCC - VB)V. When VS is no longer pulled to ground, the capacitor has a potential difference of (VCC - VB)V across it. The capacitor charges to (VCC - Vb)V when the high side MOSFET is on and VS is pulled to ground. The IR2110 circuit uses VCC (not VDD), the bootstrap diode and the bootstrap capacitor to create the additional required voltage. To turn the MOSFET on fully would require at least approximately 308V with respect to ground if the drive circuit is ground referenced. If source is at 300V, then the gate can withstand up to 320V with respect to ground, which is 20V with respect to source. The gate of the MOSFET can only withstand 15V to 20V WITH RESPECT TO SOURCE. The ceramic capacitor is not required if the bootstrap capacitor is tantalum."
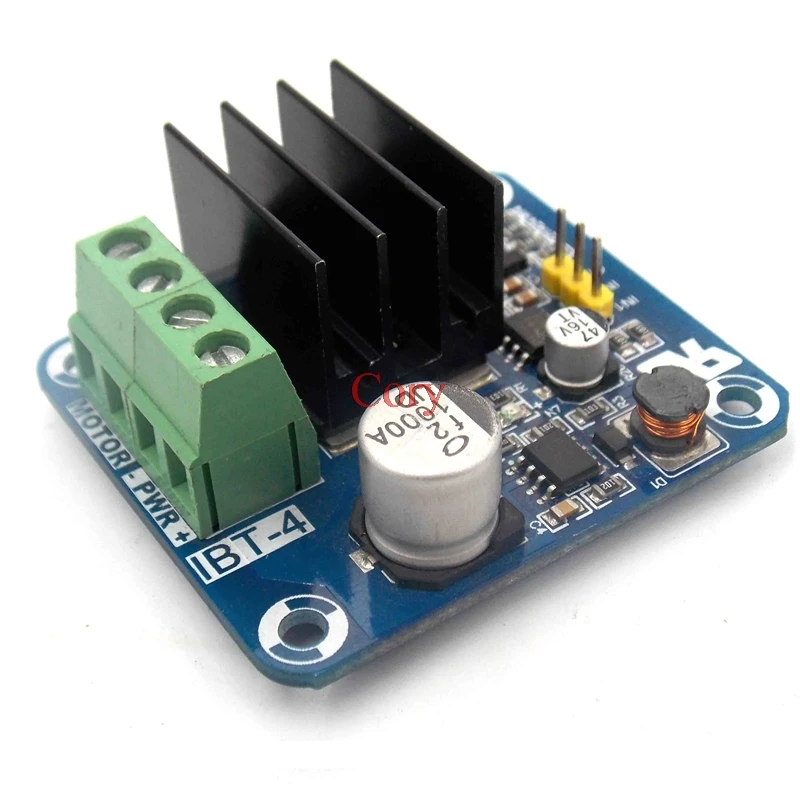
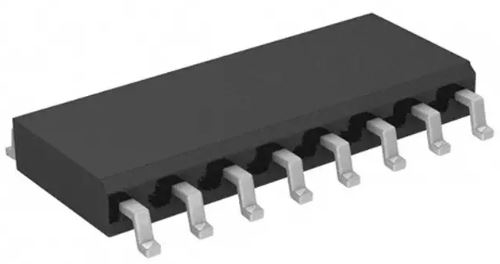
Since we’re using an electrolytic capacitor, a ceramic capacitor should be used in parallel with this capacitor. For high frequencies like 30kHz to 50kHz, I use between 4.7♟ and 22♟. For low frequencies such as 50Hz, I use between 47♟ and 68♟ capacitance. So, I just estimate the required capacitance. However, there are many parameters involved, some of which we may not know – for example, the capacitor leakage current. Yes, there are formulae available for calculating the capacitance. The higher the duty cycle, the higher the required capacitance for C1. Thus, the lower the frequency, the higher the required capacitance for C1. The higher the on time, the higher the required capacitance. C1 must also not be too large that charging is too slow and the voltage level does not rise sufficiently to keep the MOSFET on. "A large enough capacitance must be chosen for C1 so that it can supply the charge required to keep Q1 on for all the time. For simplicity I am posting the capacitor related section here: You can find it in the paragraph right below Fig. I have talked about the capacitor in the article/tutorial. The ceramic capacitor is not required if the bootstrap Since we’re using anĮlectrolytic capacitor, a ceramic capacitor should be used in parallel with Like 30kHz to 50kHz, I use between 4.7 ♟ and 22 ♟. For low frequencies suchĪs 50Hz, I use between 47 ♟ and 68 ♟ capacitance. Involved, some of which we may not know – for example, the capacitor leakageĬurrent. Yes, there are formulaeĪvailable for calculating the capacitance. The higher the dutyĬycle, the higher the required capacitance for C1. The frequency, the higher the required capacitance for C1. Slow and the voltage level does not rise sufficiently to keep the MOSFET on. C1 must also not be too large that charging is too A large enoughĬapacitance must be chosen for C1 so that it can supply the charge required to Source level of Q1 to drive the Q1 in high-side configuration. The C1 and C2 is used to add the extra voltage – VB in this case – above the When LIN = 1 and Q2 is on, C1 and C2 get charged to the level on VB, The converter is working from a 240 V power supply of a single phase ac source with a firing angle of 60 0.D1, C1 and C2 along with the IR2110 form the bootstrapĬircuitry. The armature current's value is 8 A without any ripple, and the armature resistance is 3 ohm. The back emf constant of the motor is 0.30 V/rpm. The rated speed of 1200 rpm voltage across the motor armature,Īt rated toque, armature current will also be rated that is 30 A because the current is directly proportional to the toqueĤ2) A single-phase half-controlled rectifier is driving a separately excited dc motor. Rated speed (N 2) = 700 rpm and V s=280 V Voltage across the armature (V a1) = 240 V
